Previous Molds making and Free products design
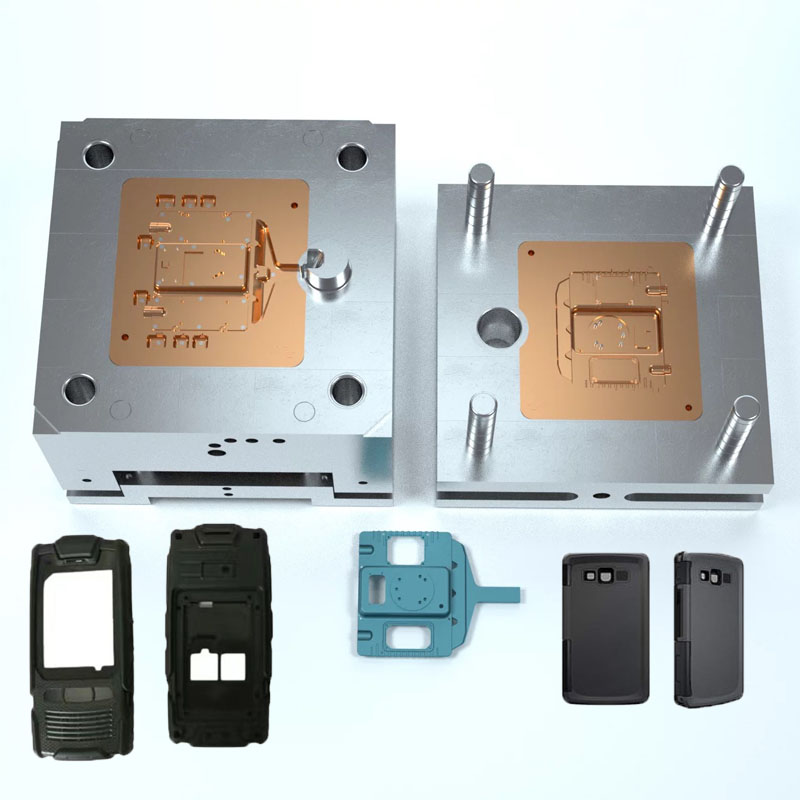
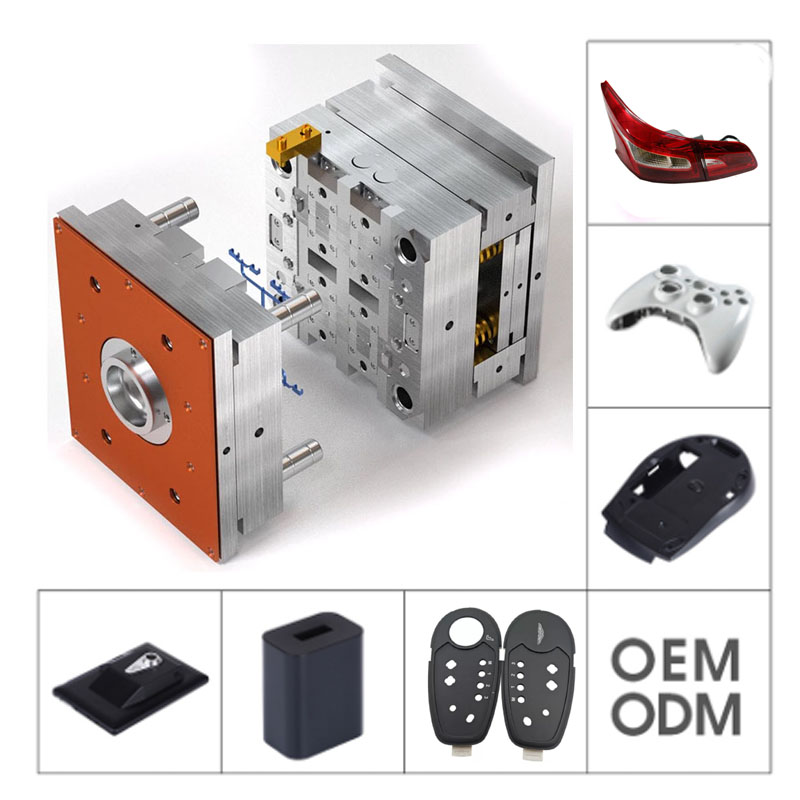
Plastic Injection Molding Parts - Design & Production for Your Needs
In our company, we pride ourselves on providing first-class service in the field of plastic injection molded parts manufacturing. With our high-precision manufactured molds and cutting-edge injection molding technology, we are able to mass produce plastic parts with ease. Our team of highly skilled engineers is dedicated to the timely manufacture of high performance plastic injection molded parts. With previous experience, we have successfully manufactured molds for various industries, including home appliances, toys, 3C electronic products, auto parts and daily necessities, etc. In addition, our monthly production capacity enables us to produce 200 sets of precision molds and inject 200,000-500,000 pieces of plastic parts.
When manufacturing injection molded parts, precision and quality are of the utmost importance. Understanding the importance of these factors, our company invests in the latest technology and machinery to ensure that we deliver products that meet our customers' expectations.
One of our strengths lies in the high precision molds we manufacture. These molds play a vital role in the injection molding process as they determine the final shape and quality of the part. Our engineers have mastered the art of mold making, ensuring that each mold is carefully designed and crafted to meet our customers' specifications. Whether it is a complex or simple design, our team has the expertise to create molds that produce high quality plastic parts.
In addition to our expertise in mold making, we have invested in state-of-the-art injection molding machines. These machines are equipped with advanced features that allow us to produce plastic parts more efficiently and accurately. With the help of these machines, we are able to achieve consistent results, ensuring that every part meets the required standards. Furthermore, our injection molding process is highly automated, minimizing the risk of errors and reducing production times.
Our company serves a wide range of industries, including home appliances, toys, 3C electronic products, auto parts and daily necessities. Our experience in these industries gives us an in-depth understanding of their specific requirements. This knowledge enables us to provide custom solutions that meet our customers' unique needs. Whether it is a small production run or a large project, we are committed to delivering high quality injection molded parts that exceed expectations.
When working with clients, we prioritize clear communication and understanding. From initial consultation to final delivery, we work closely with our clients to ensure their requirements are met. Our team of engineers and technicians are on hand to resolve any issues or queries that may arise. We believe effective communication is the key to a successful partnership and we strive to build lasting relationships with our clients.
In terms of production capacity, we are capable of handling large-scale projects. With a production capacity of 200 sets of precision molds per month and the ability to injection mold 200,000-500,000 plastic parts, we can meet tight delivery deadlines without compromising quality. Our efficient production processes and streamlined workflows allow us to optimize productivity and ensure our customers receive their orders on time.
In conclusion, our company is a trustworthy supplier of high-quality injection molded parts. With our high-precision manufactured molds and cutting-edge injection molding technology, we are able to mass produce plastic parts with ease. Our experience, expertise and commitment to quality make us the first choice in industries such as home appliances, toys, 3C electronics, auto parts and daily necessities. So whether you need a small-scale production or a large-scale project, our team is ready to deliver outstanding results.
Product Detail
Place of Origin | China |
Brand Name | HSLD/ Customized |
Shaping Mode | Fans Plastic Injection Mould |
Equipment | CNC, EDM Cutting off Machine, Plastic Machinery, etc |
Product Material | Steel: AP20/718/738/NAK80/S136 Plastic: ABS/PP/PS/PE/PVC/PA6/PA66/POM |
Mold Life | 300000~500000 Shots |
Runner | Hot Runner or Cold Runner |
Gate type | Edge/Pin point/Sub/Side Gate |
Surface treatment | Matte, Polished, Mirror polished, texture, painting, etc. |
Mold Cavity | Single or Multiply Cavity |
Tolerance | 0.01mm -0.02mm |
Injection Machine | 80T-1200T |
Tolerance | ± 0.01mm |
Free sample | available |
Advantage | one stop solution/free design |
Application field | Electronic products, beauty products, medical products, Home used products, Auto products, etc |
Plastic Injection Molding: A Game-changer in B-End Sectors
Introduction
Plastic injection molding has truly revolutionized manufacturing processes across various B-End industries, opening up endless opportunities for innovation and progress. In this uplifting article, we will delve into the vast and exciting world of plastic injection molding applications in automotive manufacturing, consumer electronics, the packaging industry, and healthcare. By showcasing real-life examples and supporting them with inspiring data, we will paint a vivid picture of how this versatile technique has remarkably transformed and enhanced these sectors.
Plastic Injection Molding in Automotive Manufacturing
The automotive industry has a reputation for constant innovation and improvement. From state-of-the-art engines to advanced safety features, manufacturers are always looking for ways to enhance vehicle performance and aesthetics. A revolutionary method that is changing the game of car manufacturing is plastic injection molding.
Utilizing this breakthrough process, manufacturers have seen significant production time savings of 25 % and reduced material waste by 30 % compared to traditional methods, according to the Society of Automotive Technology report. These compelling statistics underscore the disruptive nature of plastic injection molding. Not only has it revolutionized the manufacture of complex lightweight components such as dashboards, bumpers and grilles, but it has also enabled automotive designers to achieve superior shapes and details that can help improve fuel efficiency.
Plastic injection molding is a manufacturing technique that injects molten plastic into a mold cavity. Once cooled and solidified, the plastic part is ejected from the mold to form a precise and durable final product. The process has many advantages over traditional manufacturing methods.
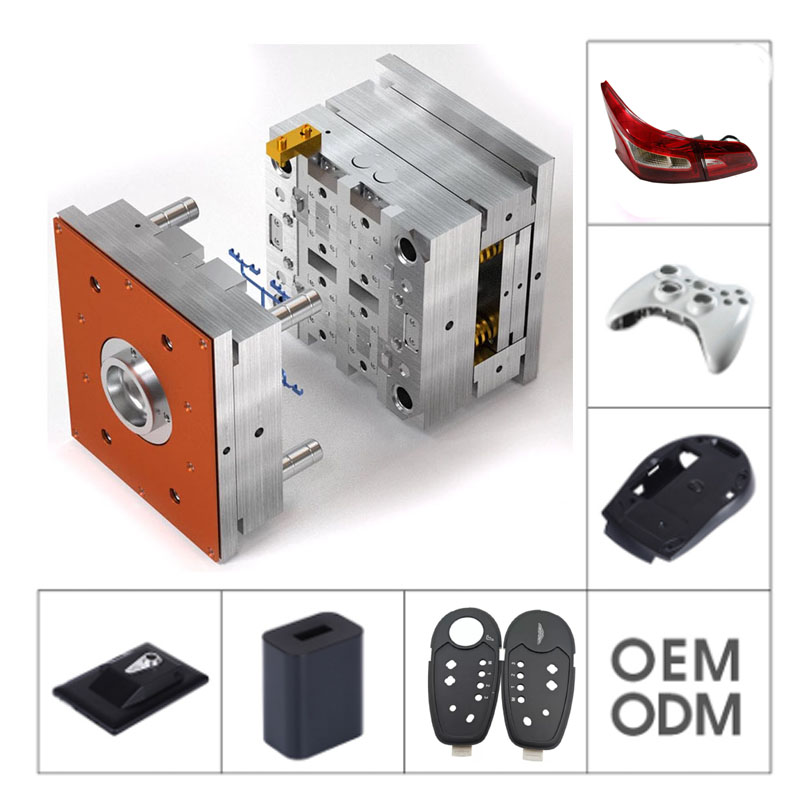
First and foremost, plastic injection molding makes it easy to produce complex parts. Using computer-aided design (CAD) software, automotive designers can create 3D models of desired components. These models are then converted into molds, ensuring that every part produced is always accurate and consistent.
Additionally, the use of automotive plastic injection molding enables lightweight components without compromising strength and durability. This improves fuel efficiency, since lighter vehicles require less energy to move. Additionally, the lightweight nature of these molded parts contributes to overall vehicle performance, including improved handling and shorter stopping distances.
Another significant advantage of plastic injection molding in automotive manufacturing is its ability to reduce material waste. Unlike traditional methods, which often involve excessive cutting and molding of material, plastic injection molding ensures that waste is minimized. Additionally, the ability to reuse leftover plastic from previous molds further underscores the sustainable nature of the process.
By adopting plastic injection molding, automakers are reaching new heights of creativity, efficiency and sustainability. This innovative manufacturing method not only changed the way automotive components are produced, but also gave designers the freedom to explore novel shapes and details. The result is visually appealing vehicles that appeal to consumers while contributing to a green future.
In conclusion, plastic injection molding has revolutionized the automotive industry. Its ability to create complex, lightweight parts with exceptional shape and detail has driven the industry forward. Not only does this approach result in significant cost savings and reduced material waste, but it also helps improve fuel efficiency and overall vehicle performance. Through plastic injection molding, automakers can continue to push the boundaries of innovation to create vehicles that not only meet consumer needs but also contribute to a sustainable future.
Injection Molding in Consumer Electronics: Changing the Industry
Consumer electronics have become an integral part of our lives, with smartphones, laptops and home appliances playing a vital role in improving our daily lives. Behind the scenes, a remarkable manufacturing process called plastic injection molding has played a major role in changing the consumer electronics landscape, enabling mass production of complex components and driving innovation in this growing industry.
Plastic injection molding has revolutionized the production process of consumer electronics, allowing manufacturers to create complex and precise designs that were previously unattainable. One particular area where plastic injection molding has had a major impact is that of electrical plastics molding. The process involves injecting molten plastic into custom molds to create seamless and durable plastic parts for electrical equipment.
Thanks to this far-sighted process, manufacturers have achieved significant savings of up to 35% in production costs(source: Electronic Manufacturers Association). By simplifying the manufacturing process and eliminating the need for multiple parts and assemblies, plastic injection molding not only reduces production time, but also increases the overall efficiency of the manufacturing process. As a result, companies in the consumer electronics industry experience faster product turnover and improved profitability.
Our company is an OEM/ODM manufacturer vendor specializing in plastic injection molds for consumer electronics. With our molds being exported to more than 20 countries, we have gained extensive experience in meeting the unique requirements of different markets. We take pride in our mold design and manufacturing capabilities, ensuring that our clients receive high-quality and reliable molds.
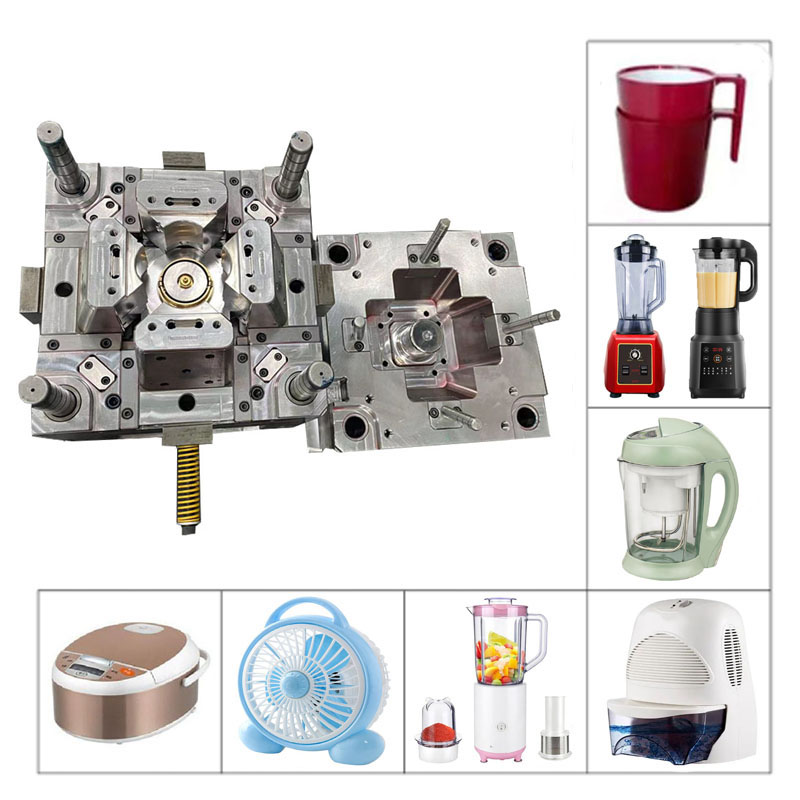
In consumer electronics, aesthetics and design play a vital role. Plastic is a highly malleable material that can seamlessly integrate innovative functions and individual designs. The ability to experiment with various materials such as polycarbonate (PC) paves the way for robust and visually appealing electronics. PC injection molding is a subtype of plastic injection molding that can produce parts with excellent mechanical properties, high heat resistance and excellent optical clarity. This has effectively raised the bar in consumer electronics, providing users with devices that not only perform exceptionally well, but are also sleek and sophisticated in design.
Plastic injection molding has pushed consumer electronics into a realm of endless possibilities. The seamlessness and efficiency of this manufacturing process allows manufacturers to meet the ever-changing demands of tech-savvy consumers. From smartphones with bezel-less displays to laptops with ultra-thin form factors, plastic injection molding has been at the forefront of creating devices that are not only technologically advanced but visually stunning.
In conclusion, plastic injection molding has transformed the consumer electronics industry. With the ability to produce complex components faster and at lower cost, manufacturers have adopted this process to bring cutting-edge devices to market. By combining innovative designs with strong materials like polycarbonate, plastic injection molding has been able to create fascinating and impressive consumer electronics. Thanks to this efficient manufacturing process, the future of consumer electronics looks brighter than ever, with a range of innovative and visually appealing devices expected to delight tech enthusiasts around the world.
Plastic Injection Molding in the Packaging Industry
The packaging industry, known for its creativity and innovation, has experienced a renaissance with the advent of plastic injection molding. By adopting this breakthrough technology, manufacturers can significantly reduce their production expenses by 40% (source: Packaging Professionals Association).
Plastic injection molding has revolutionized the way packaging solutions are manufactured, especially with preform molds, PET preform molds, plastic cap molds and preform blow molding. These molds are critical to the production of various packaging components including bottles, containers and closures.
The versatility of plastic injection molding can produce attractive packaging solutions that not only ensure product safety and longevity, but also attract consumers with eye-catching design elements. By using preform molds, manufacturers are able to create seamless and attractive bottles and containers. PET preform molds in particular produce transparent and durable packaging solutions widely used in the beverage and food industries.
Additionally, plastic cap molds can create secure and leak-proof closures for bottles and containers. These lids not only protect the contents of the package, but also provide convenience and ease of use for consumers. The precision and efficiency of plastic injection molding ensures that every cap produced is of consistent quality, resulting in a reliable packaging solution.
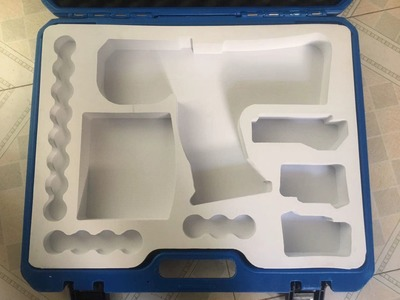
Furthermore, preform blow molding has become a popular technique in the packaging industry. The process involves injecting heated plastic material into a mold, which is then expanded with compressed air to form the hollow packaging part. Preform blow molding offers exceptional design flexibility, enabling manufacturers to create unique shapes and sizes for their packaging solutions. This not only enhances the aesthetics of the product, but also improves the consumer experience. Lightweight yet durable, these blow molded packaging solutions offer convenience and portability for consumers while reducing shipping costs for manufacturers.
Plastic injection molding paves the way for sustainable packaging solutions utilizing recycled materials. The industry is increasingly turning to environmentally friendly materials such as bioplastics, which are derived from renewable resources and can be easily recycled. By adopting plastic injection molding, manufacturers are able to reduce their environmental impact while providing innovative packaging solutions.
Companies in the packaging industry have recognized the enormous advantages of plastic injection molding and incorporated it into their manufacturing processes. These companies utilize preform moulds, PET preform moulds, plastic cap moulds, and preform blow molding technologies to produce high-quality, cost-effective and sustainable packaging solutions.
All in all, plastic injection molding has brought major changes to the packaging industry. By utilizing preform moulds, PET preform moulds, plastic cap moulds, and preform blow molding technologies, manufacturers have been able to produce compelling packaging solutions that ensure product safety, longevity, and consumer satisfaction. Furthermore, plastic injection molding facilitates the development of sustainable packaging solutions, contributing to the reduction of the industry's environmental impact. With its versatility and cost-effectiveness, plastic injection molding remains the driving force shaping the future of the packaging industry.
Plastic Injection Molding in Healthcare: Revolutionizing Patient Safety and Well-being In healthcare
Precise and reliable manufacturing processes are critical to ensuring patient safety and overall well-being. Every medical product used by healthcare providers must meet stringent standards for quality, precision and sterility. To achieve these goals, the introduction of plastic injection molding was undoubtedly a revolution. This manufacturing process has revolutionized the healthcare industry by allowing manufacturers to deliver precise, high-quality medical products. Healthcare providers have seen dramatic improvements in production precision thanks to plastic injection molding. According to the Medical Manufacturing Association, this process resulted in a significant 50% reduction in product defects(source: Medical Manufacturing Association) .
This superior quality assurance is essential when manufacturing critical medical equipment such as syringes, catheters and surgical instruments. By minimizing defects, patients and healthcare practitioners can rely on these products with confidence knowing that their functionality and safety are top priorities. One of the main advantages of plastic injection molding is the ability to ensure the sterility of medical products. In a healthcare setting, infection risk is a major concern. However, with plastic injection molding, manufacturers can produce sterile medical devices directly from the mold. This eliminates the need for additional sterilization processes, minimizing the potential for contamination and improving patient care. By reducing the risk of infection, healthcare facilities can provide a safer environment for patients, ultimately promoting their recovery and well-being.
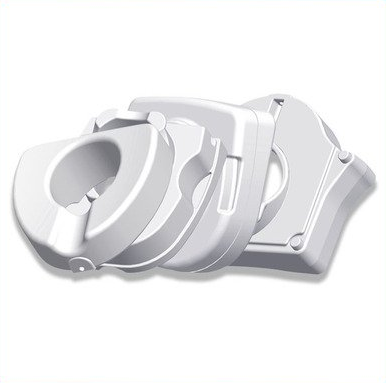
In addition, plastic injection molding enables the precise and efficient production of complex medical devices. The versatility of this manufacturing process enables the creation of complex designs, ensuring medical products assemble seamlessly and perform flawlessly. Whether it's complex surgical instruments or precisely calibrated syringes, plastic injection molding enables manufacturers to meet the demanding demands of the healthcare industry.
This precision and efficiency not only benefits patients, it also helps save costs for healthcare providers and makes quality care more accessible to a wider population. The impact of plastic injection molding on healthcare extends far beyond the manufacturing process itself. By utilizing this advanced technology, the global healthcare industry is raising the bar of excellence. As precision and reliability become the norm, the overall quality of medical products improves, leading to better patient outcomes. From reducing the risk of infection to minimizing product defects, plastic injection molding plays a vital role in saving lives and improving the overall standard of patient care. As the healthcare industry continues to evolve, so does the need for precise, reliable medical products. Plastic injection molding directly addresses these needs, giving manufacturers the tools they need to deliver exceptional quality and sterility. The transformative power of this manufacturing process allows healthcare providers to focus on what matters most: the health and well-being of their patients.
In conclusion, plastic injection molding has become a game changer in healthcare manufacturing. It enables the production of high-quality, precise and sterile medical products, reducing the risk of infection and enhancing patient care. Through this process of change, the healthcare industry around the world is saving lives and raising the bar of excellence. With the growing need for better patient outcomes, plastic injection molding will undoubtedly play a major role in shaping the future of healthcare manufacturing.
Conclusion
Plastic injection molding has ushered in an era of boundless opportunities and transformative innovation across B-End industries. By showcasing real-world examples and backing them with compelling data, we have witnessed the remarkable impact of this technique in automotive manufacturing, consumer electronics, the packaging industry, and healthcare. The cost savings, enhanced designs, and improved production precision offered by plastic injection molding have revolutionized these sectors, leaving an indelible mark on their progress and growth. As we embrace the limitless possibilities of plastic injection molding, we witness a bright future filled with endless potential for manufacturing excellence and consumer satisfaction.
So, let us embark on this remarkable journey, where creativity, efficiency, and sustainability collide through the powerful medium of plastic injection molding. Together, we can shape a world where innovation knows no bounds, and every industry thrives with the help of this incredible technology.
Feel free to contact us anytime ! We're here to help and would love to hear from you.
Factory Details
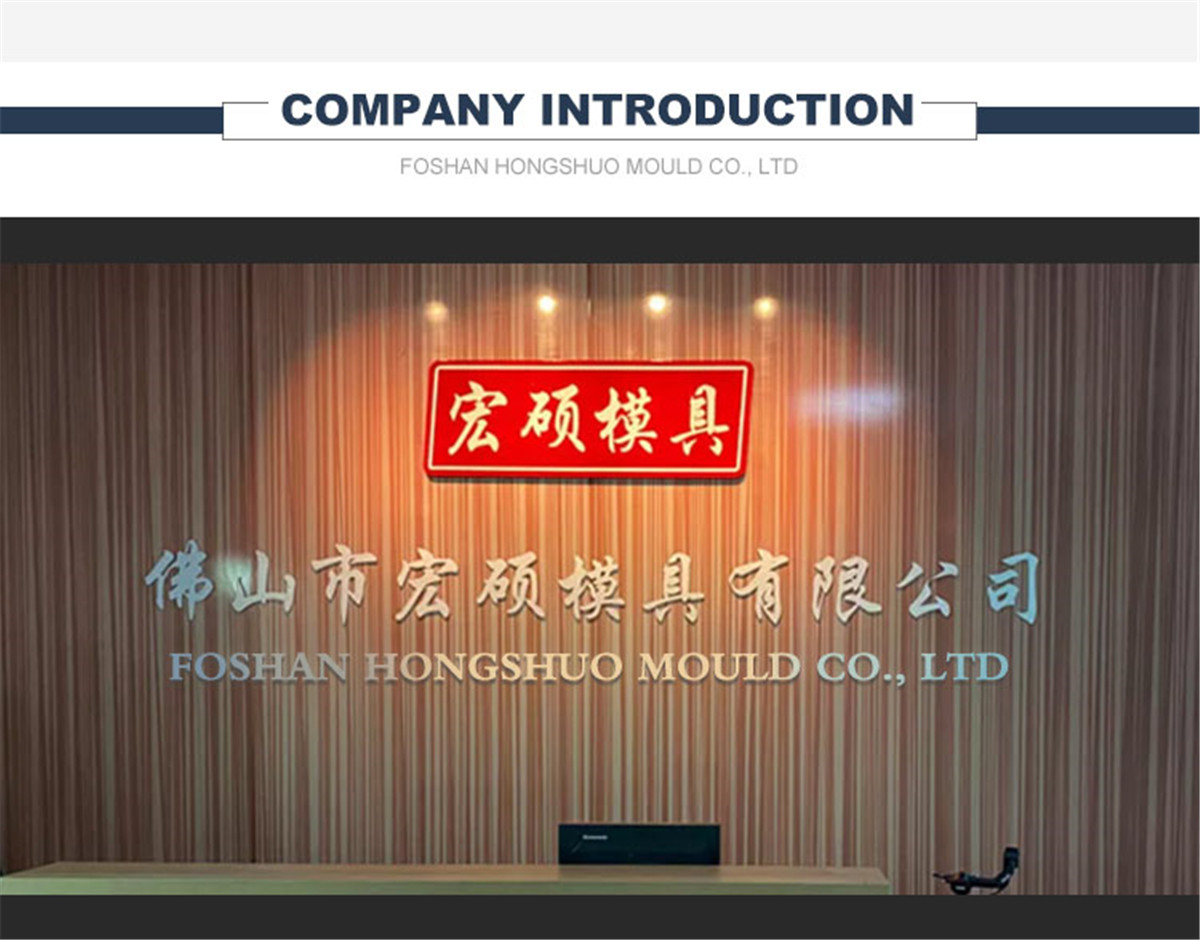
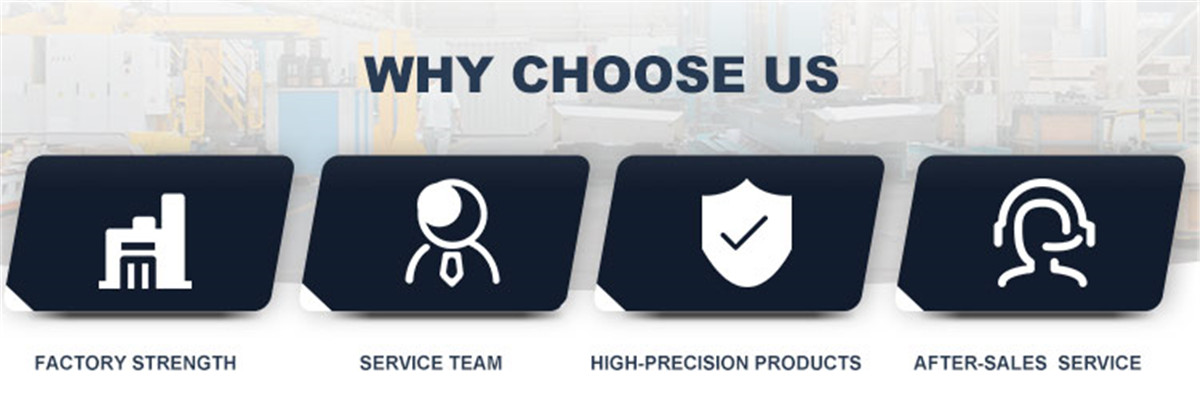
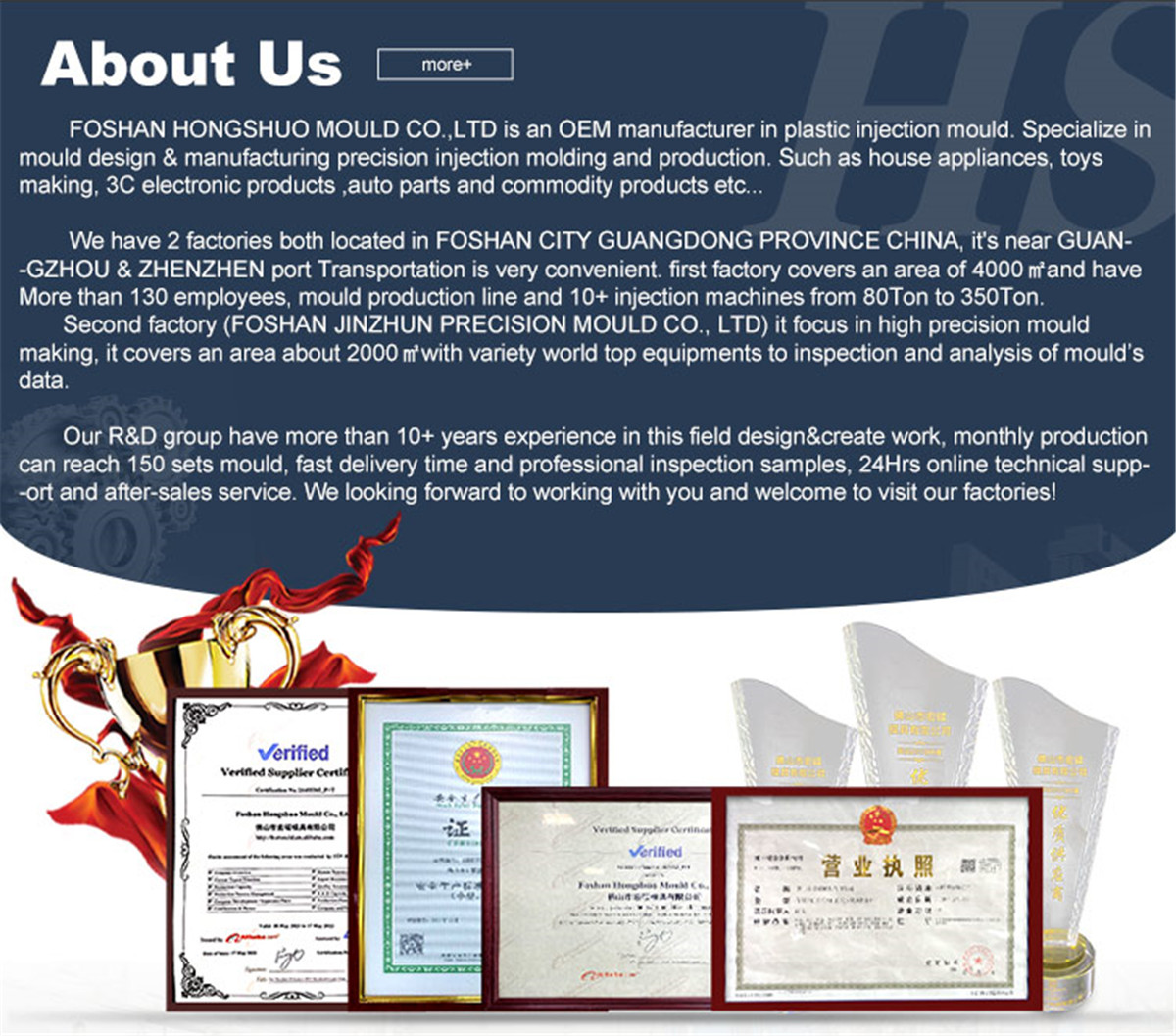
More Molds
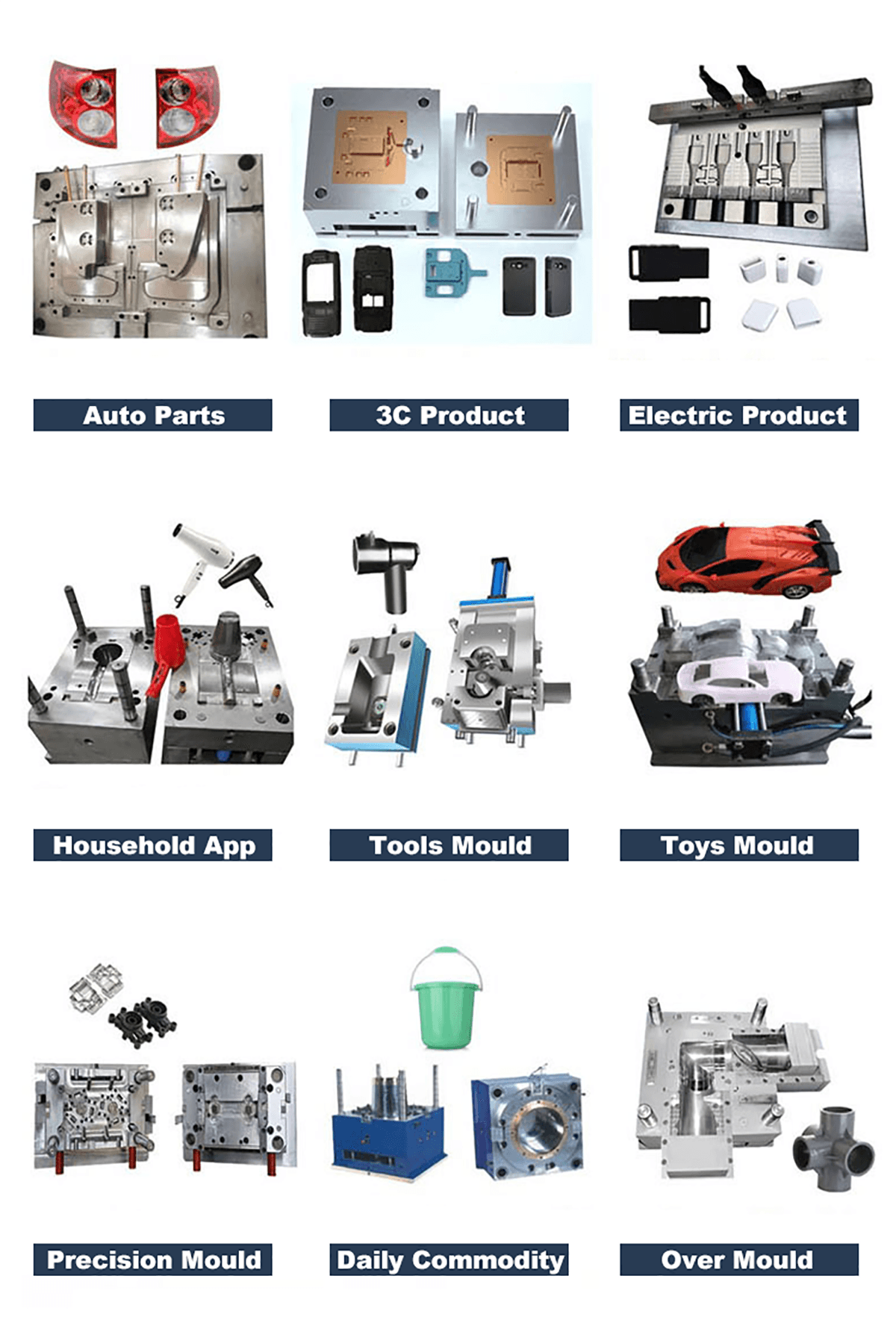
Shipment
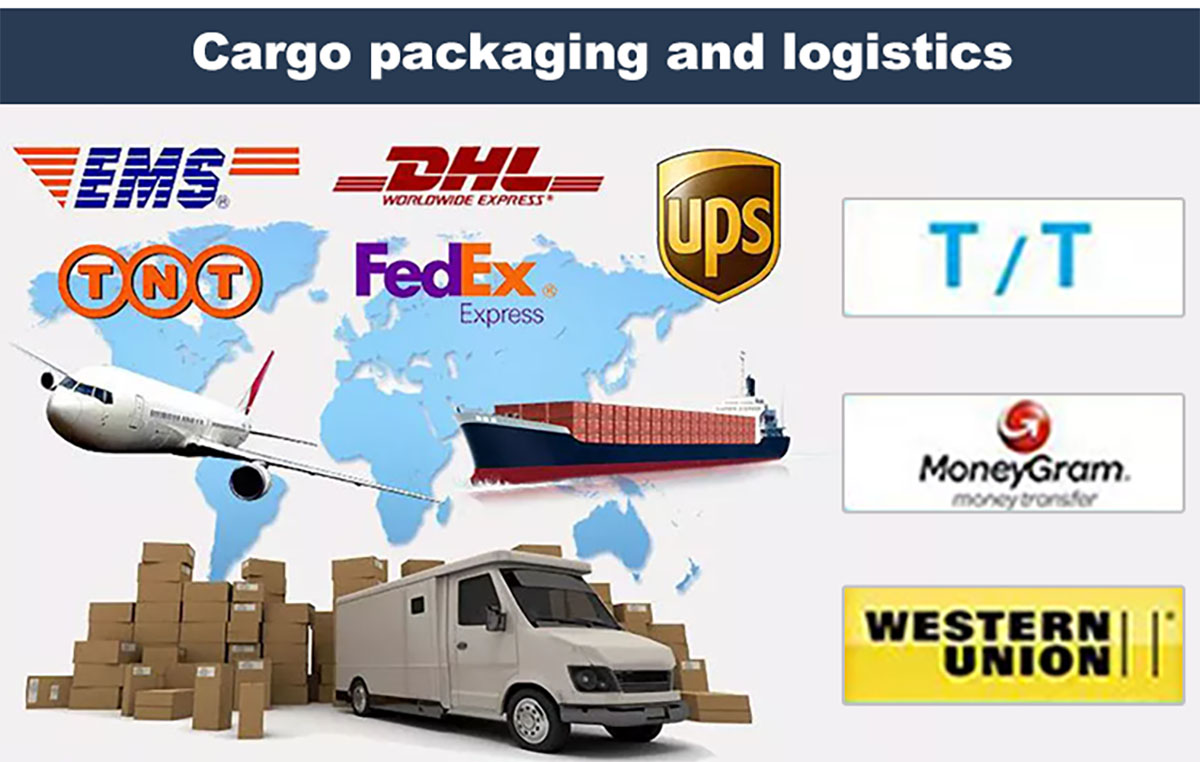
Special packaging service for you: Wooden case with film
1. To better ensure the safety of your goods, professional.
2. Good to environment, convenient and efficient packaging services will be provided.
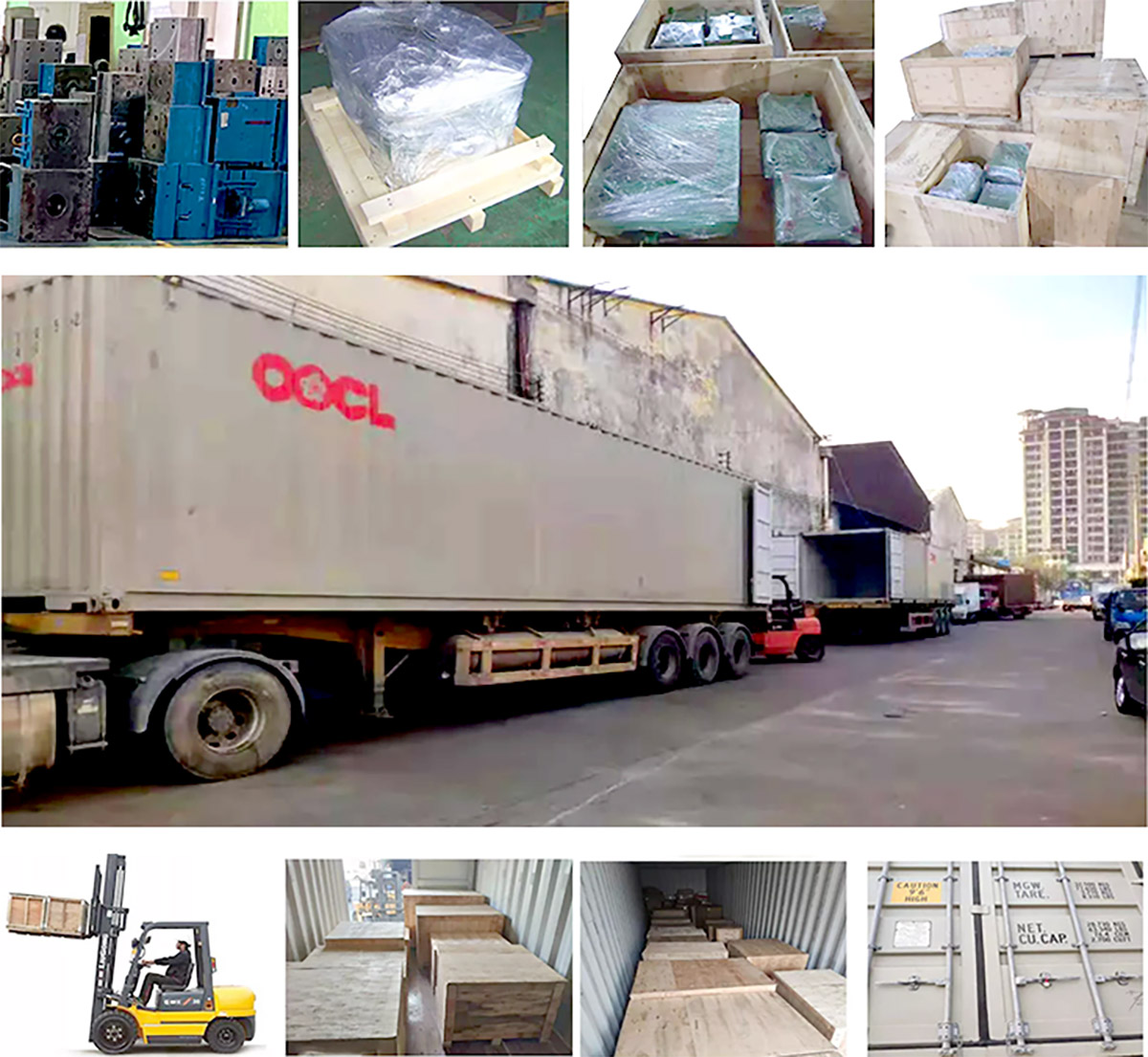
FAQ
HSLD: Yes, normally the spare parts for die casting mould we have mould insert, mould frame, window core, moving core, head of nozzle. You can check and inform what spare parts you need.
HSLD: Our mold insert is made of DAC.
HSLD: Our moving core is made of FDAC.
HSLD: Yes.
HSLD: Different equipment has different accuracy, generally between 0.01-0.02mm